The Use of Pneumatic Butterfly Valve in Different Medium
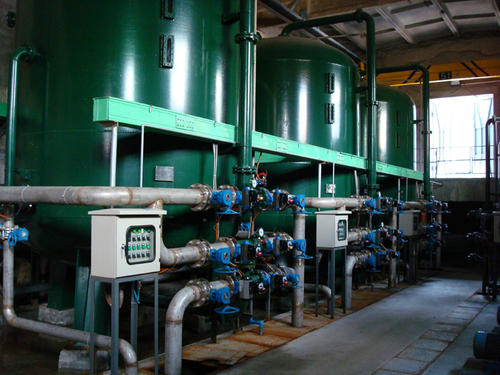
When the sanitary butterfly valve is used for the control of solid materials, it’s often used at the bottom of cans as a discharge valve. Since dust materials mostly contain particles large and small, the wear on the valve sealing surface is a sure thing. Improper selection of the model will greatly reduce the service life of the valve, or soon lead to leakage within the valve, affecting normal use.
Usually, in the PLC program, we prolong the motor vibration time in order to knock all materials out before closing the valve. Adjust the zero gauge of the weighing instrument, which displays zero after all the materials are knocked out when PLC sends a signal of closing the valve.
Replace triple eccentric butterfly valve with double eccentric elastic hard sealing butterfly valve. Since the valve seat of the triple eccentric butterfly valve is a slanted sealing surface, the materials can easily accumulate on the sealing surface, not being able to be quickly discharged.
In contrast, a single eccentric or double eccentric butterfly valve doesn’t have such a disadvantage. Even if there’re some materials on the sealing surface, they’re scraped off by the valve plate when the valve closes, ensuring good sealing and durability of the sealing surface.
In such a system, there’re other factors that need to be taken into account. For example, we can’t let the material rush directly into the valve plate. Also, the static pressure of the material must not exceed the designed pressure tolerance of the pneumatic butterfly valve.
The difference between a regulating valve and a conventional manual valve is that you can’t regard the regulating valve as an isolated component. Rather, it must be considered as part of the entire automatic control system.
Many of the problems in the use of regulating valves are not problems of selection and configuration but are because of users’ lack of understanding of regulating valve, leading to the inability of regulating valve to work well with the control system.
As long as the key to the problem is identified, correct selection of the valve and good debugging at the system debugging phase can greatly reduce the failure rate, making the automatic control system run stably in the long run.