Pressure Testing Methods for Gate Valves
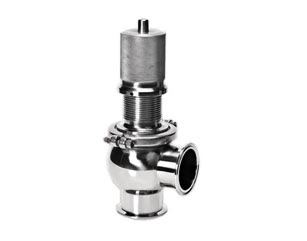
What is a Gate Valve?
Gate valves are commonly used valves that completely shut off fluid flow by moving a gate-like barrier into the pipeline path, creating a powerful seal. In the fully open position, gate valves completely remove the gate from the fluid path, which runs straight through the valve causing very little to no loss in flow rate or flow volume.
Due to their construction design, sanitary gate valves are quite slow to actuate — it takes several full rotations of the knob or wheel handle actuator to change the gate’s position. This quality makes them suitable only for applications with infrequent on/off switching. If you need a fast-actuating valve with other similar qualities, consider using a ball valve instead.
How does a gate valve work?
The opening and closing member of a flanged gate valve is the gate plate. The gate plate moves perpendicular to the pipeline’s fluid flow direction. Gate valves can only be used in the fully open or fully closed positions; they are not suitable for regulation and throttling.
The gate valve’s closing mechanism is the sealing surface of the gate plate and valve seat, which are highly smooth, flat, and consistent. They adhere directly to each other, creating a dependable seal that prevents the medium from flowing through the valve. They rely on the shape of the top mold, the spring, or the gate plate to enhance the sealing effect.
Applications: The uses of gate valves
Gate valves are mainly used to cut off flow through the pipeline. They offer very little fluid resistance because the valve’s opening is typically the same diameter as the pipeline. In this sense, it can be described as a straight-through flow valve. It can be used in circumstances where the medium flows in both directions. It is not directional, so the sealing surface is not prone to erosion when the valve is fully open. A wide variety of gate valves are made in different DN sizes; they are commonly manufactured in DN50 up to DN1050.
Gate valves are used in several applications like process manufacturing, automotive, oil & gas, pharmaceutical, and marine industries. Gate valves are also one of the most widely used valves in water supply systems.
How to Pressure Test a Gate Valve: Three Methods
The strength test of the gate valve is the same as that of the sanitary shut-off valve. There are two types of sealing performance tests for gate valves.
Standard Gate Valve Test Method:
- Open the gate plate.
- Allow the pressure inside the valve to rise to the specified test value.
- Close the gate plate.
- Immediately remove the gate valve to check for leakage on both sides of the gate plate sealing. If you find any leakage, immediately replace the valve with a new one.
Alternate Gate Valve Testing Methods
Middle-Pressure Test:
- Alternatively, you can directly instill the test medium into the plug on the valve cover to the specified value.
- Check the sealing at both sides of the gate plate. This method is not applicable in gate valves whose nominal diameter is less than DN32mm.
Blind Plate Test:
- Open the gate plate.
- Allow the system pressure in the valve to rise to the specified value.
- Close the gate plate.
- Open the blind plate on one side to check the sealing surface for leakage.
- Repeat the test until it is qualified.
The sealing performance test of the pneumatic gate valve stuffing and gasket should be carried out before the valve’s sealing performance test.
Conclusion
Thank you for reading our article, and we hope it can help you better understand the pressure testing methods for gate valves. If you want to learn more about sanitary valves, please visit Adamant Valves for more information.