The Improvement on Sealing Structure of Shut-off Valve
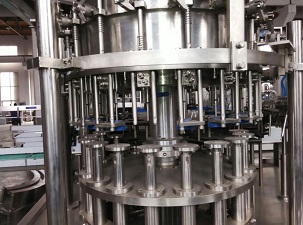
The shut-off valve has a simple structure. It can open or shut off the valve and ensure the valve’s sealing and upper sealing function through the mechanism of the valve stem being able to both rotate and lift.
Due to the special movement mechanism of this type of structure, it has adverse consequences on the upper sealing pair of the sanitary shut-off valve (there’s the vertical pressure required for the sealing pair, and there’s the relative sliding friction between sealing pairs).
The practice has proved that after several times of opening and closing of the upper sealing of the shut-off valve, leakage will be caused due to scratches between sealing pairs. Valves with slight scratches will need to be disassembled and repaired.
Valves with severe scratches will have to be abandoned due to serious damage. Such results not only increase the manufacturing cost of companies but also affect the performance of the valve. In order to solve these kinds of problems, the structure and materials of the upper sealing of the shut-off valve are tested and improved.
1. Move the upper sealing part of the valve stem onto the valve flap.
The purpose is to make the upper sealing surface on the valve flap to be in a static state without slipping relative to the upper sealing surface of the valve cover.
Although such an improvement can improve the service life of the upper sealing, it’s not cost-effective because of the fact that there needs to be a sealing between the valve flap cover and the valve flap.
2. Change the materials of the upper sealing pair.
Solder the sealing cone surface of the valve stem with Stellite hard alloy that has a good anti-scratch performance. This method has achieved good results. However, on the one hand, because the cost of Stellite hard alloy is too high, and on the other hand, because the material of the valve stem is martensitic stainless steel, the solderability is poor. There needs to be a pre-heating before soldering.
The temperature-keeping and welding techniques after soldering are complex. In addition, to ensure the dimensional precision of the valve stem, the rough-processing procedure needs to be added.