The Classification of Steel Gate Valves
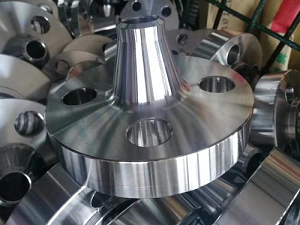
What are the types of gate valves?
Gate valves can be divided into two main types: Parallel and wedge-shaped.
The Classification of Steel Gate Valves
1. According to the structure of the gate plate
1) Parallel gate valve: the sealing surface is parallel to the vertical centerline. Two sealing surfaces are parallel to each other. A parallel gate valve usually uses a double gate plate structure.
Among parallel gate valves, the structure with the thrust wedge is the most common. This kind of sanitary valve is suitable for low-pressure medium and small diameter (DN40-300mm) valves. There’s also a kind of valve that has a spring between two gate plates. The spring can produce a tightening force, which is conducive to the sealing of the gate plate.
2) Wedge gate valve: There’s a certain angle formed between the sealing surface and the vertical centerline, that is, a gate valve whose two sealing surfaces form a wedge.
The angle of inclination of the sealing surface is generally 2°52′, 3°30′, 5°, 8°, 10°, etc. The angle mainly depends on the temperature of the medium. Usually, the higher the operating temperature, the greater the angle. This is to reduce the possibility of wedging when the temperature changes.
Among wedge gate valves, there are single gate plates, double gate plates, and elastic gate plate valves. Single gate plate wedge gate valve has a simple structure and good reliability. But it has a high requirement for the precision of the angle of the sealing surface. And it’s quite difficult to process and repair it. It’s prone to clamping and abrasion. And there’s a high possibility that it’s going to be wedged when the temperature changes.
The double gate plate wedge gate valve has a rather complicated structure and is mostly used in pipelines of water and vapor medium. Its advantages: it has a low requirement for the precision of the angle of the sealing surface; there’s a low possibility that it’s going to be wedged when the temperature changes; when the sealing surface wears, the gasket can be added to compensate for it. But this kind of structure has many parts, which are prone to adhesion in a viscous medium, affecting the sealing.
More importantly, the upper and lower baffles are prone to corrosion due to long-term use, the gate plate is easy to fall off. The elastic gate plate wedge gate valve has an annular groove around the periphery of the gate plate, which makes the gate plate somewhat elastic. It shares the advantages of a single gate plate wedge gate valve of simple structure and good reliability. It can also produce slight elastic deformation to compensate for the deviation that occurred during the processing of the angle of the sealing surface to improve the technique. It has now been widely used.
Gate valves of special purposes, such as large diameter gate valves used in pipelines of long-distance oil and gas supply, use single gate plate structure due to the need to clean the valve and pipelines.
2. According to the structure of the valve stem
1) Rising stem gate valve: the nut of the valve stem is on the valve cover or bracket; When switching the gate plate, turn the nut of the valve stem to lift the valve stem. This structure is beneficial to the lubrication of the valve stem, with obvious opening and closing, so it’s widely used.
2) Non-rising stem gate valve: the nut of the valve stem is inside the valve body and directly in contact with the medium. Turn the valve stem to open or close the gate plate. The advantages of this structure: the height of the gate valve always remains unchanged, so the room for installation is small.
It’s suitable for large diameter gate valves or gate valves that have limited room for installation. An opening and closing indicator need to be installed in this structure to indicate the degree of opening and closing. The disadvantages of this structure: the valve stem thread not only can’t be lubricated but is directly eroded by the medium, which makes it easy to be damaged.
3. The diameter contraction of the gate valve
If the diameter of a channel in a valve body is not the same, it’s known as diameter contraction. It can reduce the size of the parts and the force needed to open or close the valve, expand the scope of applications of parts. But after diameter contraction, the loss of fluid resistance increases.
In certain working conditions of certain departments (such as oil pipelines of the petroleum department), valves of diameter contraction are not allowed to be used. On the one hand, this is to reduce the loss of resistance of the pipelines, on the other hand, this is to avoid impeding the mechanical cleaning of pipelines after diameter contraction.