How To Install a Safety Valve?
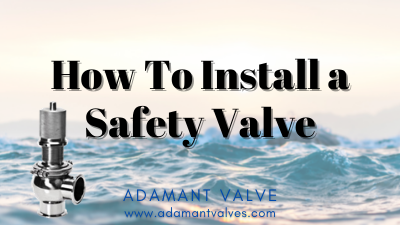
Always use correct installation techniques and take necessary precautions when installing a safety valve. Proper safety valve installation is critical to the safety of your employees and your fluid or air-gas processing system.
Where Should a Pressure Relief Valve be Installed?
The safety valve should be installed as close as possible to the protected equipment or pipe. If the valve can’t be installed close to the layout, then the pipe’s pressure drop from the protected equipment’s inlet to the valve inlet must not exceed 3% of the sanitary valve’s constant pressure.
The safety valve should be installed in places where it’s easy to maintain and regulate, and there should be enough workspace around it to make convenient repairs in the future. The safety valve should not be installed at dead ends of horizontal pipes, so that solid or liquid materials don’t accumulate and affect the normal operation of the valve.
How To Install a Safety Valve?
Should a Safety Valve be Installed Horizontally or Vertically?
Safety valves within equipment or piping systems should be installed upright. But for safety relief valves installed in liquid pipes, heat exchangers, and containers, when the valve is closed, in occasions where the pressure may increase due to thermal expansion, they can be horizontally installed.
What Pressure Should a Safety Valve be Set To?
Safety valve settings are usually set at least 10% above the system’s maximum operating pressure. If your system is designed to tolerate some unstable pressure conditions, you can use a setting of 25-PSIG above the maximum operating pressure.
In fact, the design of the safety valve should take into consideration the fact that the back pressure doesn’t exceed a certain value of the constant pressure of the valve. For instance, for an ordinary spring safety valve, its backpressure does not exceed 10% of the constant pressure of the valve.
Precautions for the Inlet, Outlet, & Discharge Pipes
- The safety valve inlet pipe should use a long radius elbow.
- The safety valve outlet pipe buried into a closed system should follow the flow direction of the medium and be connected to the top of the pressure relief pipe at a 45-degree slant. This is to prevent the condensate in the general pipe from flowing back into the branch pipe.
- When the outlet pipe is long, a certain slope should be set up to ensure efficient drainage by gravity (except for dry gas systems).
- For the safety of all, the safety valve discharge pipe cannot be directed towards equipment, platforms, ladders, cables, and so on. Discharging excess pressure can cause injuries.
- There should be a “bag-shaped” liquid container inside the discharge pipe of the wet gas pressure relief system.
Other Precautions to Take When Installing Safety Valve
- For large-diameter safety valves, we need to consider the possibility of lifting after disassembly. If necessary, a lifting stem can be used.
- The installation height of the safety valve should be higher than that of the pressure relief system. If the valve outlet is lower than the pressure relief general pipe or the discharge pipe needs to be lifted up to be connected to the general pipe, we should set dispensers at low and accessible points.
- When there’s a shut-off valve on the outlet pipe of the safety valve, a single gate plate or gate valve should be used. The valve stem should be horizontally installed in order to prevent the valve plate from slipping down when the pin connecting the valve stem and valve plate is corroded or loose.
- When the safety valve is installed with a bypass valve, the valve should be sealed.
Thank you for reading these instructions on how to install a safety valve. We hope it can help you to better understand the precautions to take when installing a safety valve. If you want to learn more about safety valves or other types of sanitary valves, please visit Adamant Valves homepage for more information.