Packing Failures and Troubleshooting for Sanitary Pumps
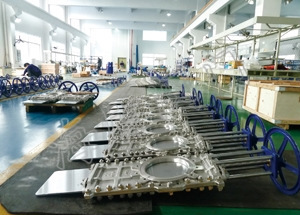
Why Packing Fail
Generally, the packing of a sanitary pump fails for two reasons: normal deterioration and improper usage (usually considered as premature failure).
Normal Deterioration
Packing is designed to wear and tear due to pressure and lubricant consumption. With normal usage, a portion of lubricant in the packing material would lose. This is normal and is expected.
Premature Failure
Premature failure refers to that a packing stops working within the expected lifetime. For sanitary pumps, good packing conditions are an important factor to ensure the product’s quality. It is the right issue that deserves enough attention when selecting s packing and operating a pump.
There are four main causes of premature packing failure:
- Improper selection of packing materials or sizes. This can be solved only by checking with the manufacturer.
- An excessive amount of abrasive materials entering the stuffing box from the pumped fluid or not removed by the flushing action of the seal water.
- Pump runout, vibration, or other similar conditions caused by bad bearings, worn or damaged shaft, loose base bolts, misalignment, imbalanced motor, etc.
- Seal water shortage or packing lubricant loss, which will cause the packing to burn and thus be destroyed.
With regard to the premature lubricant loss, it is possible to be caused by the excessive pressure exerted on the stuffing box. When pumping at high pressure, it is necessary to apply considerable pressure on the packing. However, this need can be alleviated by reducing the pressure differential between the stuffing box and the atmosphere.
How to make it? Just installing a bypass line with a throttling valve in the seal water line and exiting this line to the atmosphere will be enough. By adjusting the throttling valve you can regulate the stuffing box leakage and extend the packing life.