Overview of the Sanitary Pump
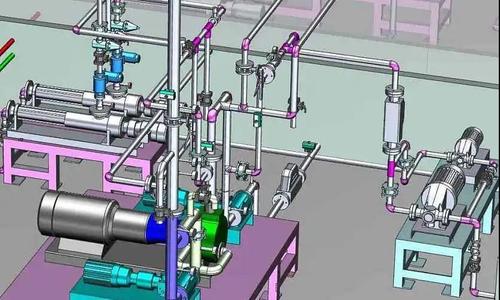
Food processing is mainly divided into three major processes, namely incoming material, semi-finished product processing, and finished product, in which each part is more or less involved in the sanitary pump. For example, chocolate processing needs pumps capable of conveying high viscosity media, wastewater treatment needs pumps that are resistant to abrasion and corrosion, and pharmaceutical preparation needs pumps with good corrosion resistance. For different product manufacturers, the pump materials required at different stages are also different.
Sanitary pumps are mainly used for filling, emptying, batching, and mixing. Besides that, it is used to transfer process fluid from equipment such as membrane filters. At present, the sanitary pump industry is relatively mature, and the main manufacturers of such pumps include Alfalaval, Bominox, CSF, SPX, Grundfos, and so on.
There are many types of sanitary pumps, which are determined by the diversity of the media they deliver. From clean straight drinking water to milk and jam, these materials are acidic, alkaline, easy, or hard to flow. The main types of sanitary pumps are centrifugal pumps, CAM pumps, single-screw pumps, and peristaltic pumps, and their design methods are largely the same but not exactly the same as ordinary pumps. Taking the centrifugal pump as an example, the following points need to be paid attention to are briefly explained.
There is no blind Angle in the flow
In the food production process, the medium in contact with the pump needs to be flowing. However, the mechanical seal cavity in the normal pump is usually a dead Angle, and the open or conical seal cavity is required.
Weld surface roughness
The surface roughness of the weld shall be 3.2, and the general surface shall be 0.8, that is to say, the pump body flow channel and the impeller flow channel need to be polished. It is difficult for ordinary cast parts to meet this requirement, so the centrifugal sanitary pump generally adopts the stamping and welding structure. Sometimes, the impeller is open or half-open.
Meet the CIP requirements
Most production lines need to be flushed once a day to remove residue that can deteriorate and cause bacteria, while many use clean water for a period of pumping or backwashing. In a flush time period, the slow flow of the medium (such as the sealing cavity of the material) should all flow out.