Maintaining Sanitary Diaphragm Valves
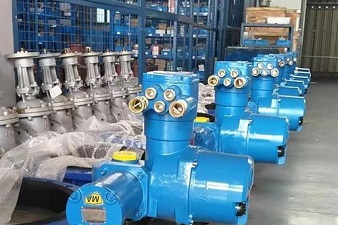
The biopharmaceutical industry relies on sanitary diaphragm valves for its demanding process applications due to a unique need for cleaning and drainage, and pressure with temperature capabilities. Over the past 40 years, the basic design of these valves has remained the same: body, diaphragm, top works, and four fasteners. Proper installation and maintenance of these valves require experienced personnel and rigorous service practices to ensure consistent and reliable valve performance.
How to Maintain Sanitary Diaphragm Valves?
Sanitary diaphragm valves act both as a gasket and dynamic seal. They are often exposed to harsh chemicals, high temperatures, and high pressures, resulting in significant wear and an increased need for routine maintenance. Proper valve maintenance requires several steps on the part of the maintenance team to ensure that the valve will operate at its full potential.
Valve/installation assembly.
One of the most important elements of maintenance is a good fitting when replacing the diaphragm. Failure to assemble the valve properly may result in batch contamination, poor valve performance, and a short life cycle. Proper installation of the diaphragm according to the manufacturer’s instructions is essential. If the installation is incorrect, excessive force during operation may damage the diaphragm. The fluids can then pass through the closed valve or, in the worst case, cause a catastrophic failure that results in fluid contamination and leakage. Tightening and retightening are also important steps in the assembly process that can often lead to seal failure, either by making the seal too tight or too loose for proper performance.
Replacing the diaphragm.
Another aspect of valve maintenance is knowing when a replacement diaphragm is needed. To ensure that the valves do not fail, some companies regularly change the diaphragm (eg every six months), whether necessary or not. Facilities that use diaphragms with shorter life expectancy, such as rubber diaphragms, may be more likely to require more regular changes. However, constant replacement of diaphragms without any sign of failure can cost factories unnecessary time and money. Knowing the signs of a valve failure is also essential to maintaining the valves of an installation. Physical signs that a valve or diaphragm needs to be replaced are excessive wear, corrosion, or fluid leakage.