Introduction of Upper Sealing Structure of Shut-off Valve
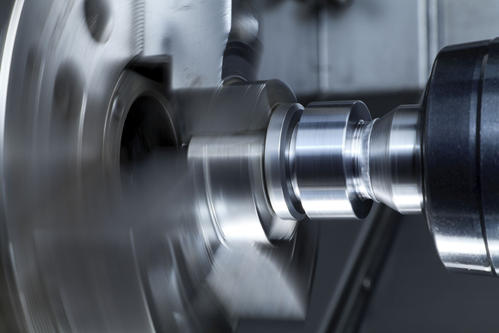
The shut-off valve has a simple structure. It can be opened or shut off through the mechanism of the valve stem rotation and lifting. And the sealing and upper sealing functions of the valve can be ensured.
Due to the special movement mechanism of this structure, it will cause extremely unfavorable consequences to the upper sealing pair of the valve (the formation of mandatory vertical pressure between sealing pairs and the friction of relative sliding between sealing pairs).
The practice has shown that after only a few times opening and closing, the upper sealing of the valve will have leakage due to the scratches between sealing pairs. Slight scratches require disassembly and repair, serious scratches result in damage and scrapping.
Such a result not only increases the cost of manufacturing for companies but also affects the performance of valves. In order to solve this kind of problem, tests and improvements are made to the structure and materials of the upper sealing of the valve.
1. Move the upper sealing part of the valve stem onto the valve flap (the purpose is to make the upper sealing surface of the valve flap be in a static and non-slip state relative to the upper sealing surface of the valve cover during the process of being under impact).
Although such an improvement can improve the service life of upper sealing, it is not cost-effective due to the fact that there needs to be another piece of sealing between the valve flap cover and the valve flap, complicating the structure.
2. Change the upper sealing pair materials. Solder Stellite hard alloy that has a good anti-scratch performance on the sealing cone of the valve stem.
This method has achieved good results. However, on the one hand, the cost of Stellite hard alloy is too high, on the other hand, the basic materials of the valve stem are 13Cr martensitic stainless steel, which has poor solderability.
There needs to be a pre-heating before soldering, and the insulation and welding technique after soldering is complicated. In addition, in order to ensure dimensional precision, a rough processing procedure needs to be added. Overall, except for special requirements, this method is also not cost-effective.
The practice has shown that improving the valve stem cone hardness is a feasible option to improve the service life of the upper sealing of sanitary shut-off valve.