How to Install Sanitary Pumps?
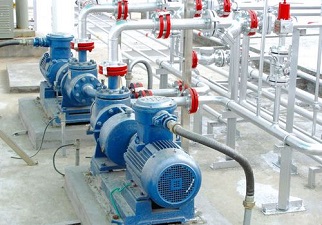
The following are the factors to consider when installing sanitary pumps:
Straight Lengths of tubes
It is of great importance to have 4-6 tube diameters of inlet tubing that is straight into the pump when installing a sanitary pump. The continuous length of the inlet enables the flow to be laminar into the pump. Preventing turbulent, choppy flow increases air entrainment. This further reduces the chances of pump cavitation. Cavitation is a major destroyer of the efficiency of pumps in PD and sanitary centrifugal pump applications. Smooth flow with fewer transitions results in better performance of pumps.
Piping Support
Sanitary tubing becomes very heavy when filled with fluid. 10 feet of 3” sanitary pipe holds about 4 gallons of fluid, in this example, water. That totals up to a weight of about 33 pounds. Such a weight is too much to hang off the pump’s end. Distribution of the weight and strain evenly is therefore necessary. This is done using hangers or other means of support. This weight can misalign the pump shafts and the motor. The result is a shaft deflection and a terrible pump failure. Excessive strain can break the seals in the system and allow air into the process.
Piping Slope
There are three reasons why the piping slope is important. First of all, it helps in the drainage of the systems when a cleaning cycle is run. Secondly, it prevents pockets of air in the suction line. Lastly, when the fluid mixes with air, it leads to cavitation and loss of efficiency of the pump. It is therefore important to slope piping in an upward manner on the inlet side of the pump, and reduce points where air can accumulate.
Strainers and Traps
Strainers and traps protect both the pump and the product. Inlet side traps and strainers can prevent damage to the pump by foreign matter. Clogging of the pump inlet can lead to flow stoppage and cavitation.
Pressure Gauges
Discharge and inlet gauges help in diagnosing and identifying problems with the pump. Gauges are the most convenient way to identify changes in product, system, or pump condition. The following are the three common types of valves in a good set-up of a pump:
- Check or foot valves – are located on the inlet. They ensure the maintenance of a liquid leg on the side of the pump that sucks. Sanitary check valves prevent backflow and keep the pump primed.
- Relief valves – protect the piping system from excessive pressure
- Isolation valves – allows for the safe removal of the pump from the piping system and maintenance of the system without having to empty the entire pipeline.
Conclusion
In conclusion, the installation of sanitary pumps in an application has many factors that need considering. First of all, the pump to be used needs to be identified by Identification of the best technology to be used, selection of the motor and drive, and many more. This leads to a successful choice and installation of the pump in a system in the best way possible.