FAQs in Using Valves
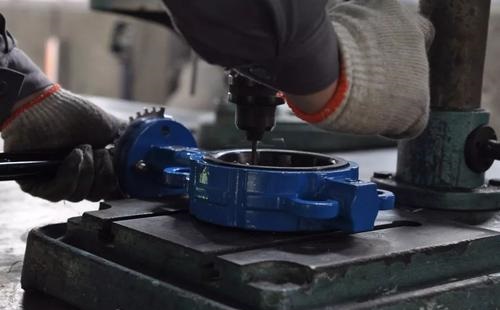
1. Why is the sanitary double seat valve easy to oscillate when working?
For single-core, when the medium is an open type, the valve stability is good; when the medium is a closed type, the valve stability is poor. The double seat valve has two spools, the lower spool in the flow closed state, and the spool in the open state. In this way, when the valve is working, the flow of the closed spool easily leads to valve vibration. This is why a double seat valve cannot be used for small openings.
2. Why double seal valve cannot be used as a shut-off valve?
The double seat valve core has the advantage of a force balance structure, allowing a larger pressure drop, but its biggest drawback is that the two sealing surfaces cannot be in perfect connection at the same time, resulting in a huge leak. If it is artificially and forcefully cut off, the effect is clearly not good. Even for it made many improvements (such as a double seal sleeve valve), is not effective.
3. Why does the straight stroke adjustment valve appear to have poor anti-blocking performance, while the angular stroke valve anti-blocking performs well?
The straight stroke adjustment valve spool is a vertical throttling, but the medium is horizontal when inflow and outflow. In this way, the flow channel in the valve cavity must be distorted so that the flow path of the valve becomes quite complicated (the shape is inverted “S”). There are many dead zones, thus providing room for precipitation of the medium. In the long run, congestion takes shape. On the contrary, an angular stroke valve is not a vertical throttling. The entrance and exit of the medium are horizontal, which is easy to remove the dirty matters. At the same time, its flow path is simple, medium precipitation space is also small, so the angular stroke valve has a better performance in anti-blocking.
4. Why is the stem of the straight stroke adjustment valve thin?
It involves a simple mechanical principle: sliding friction is large, and rolling friction is small. When the valve stem of the straight-stroke valve moves up and down, the packing is slightly compressed, and it will pack the valve stem tightly and produce a large backlash. To this end, the stem design is very small and the filler also commonly uses PTFE small friction coefficient in order to reduce backlash. However, the resulting problem is a thin stem that is easy to bend, and the filler life is also short. To solve this problem, the best way is to use the trip valve stem, that is, the type of angular travel control valve. Its stem is 2 to 3 times thicker than the straight stroke stem. And if a filler of long-life graphite is chosen, the valve stem becomes stiff. But the friction torque is small, and hysteresis is small as well.
5. Why shut-off valve should try hard seal?
The shut-off valve requires leakage as low as possible. The leakage of the soft-sealed valve is the lowest, and its cut-off effect is very good. But it is not wear-resistant, and its reliability is poor. From the double standards of small leakage and reliable seal, the soft seal is not as good as a hard seal. Such as a full-function ultra-light control valve, sealed and piled with wear-resistant alloy protection, has high reliability. A leakage rate of 10-7 has been able to meet the requirements of the shut-off valve.
6. Why is shape selection more important than calculation?
For calculation and shape selection, the latter is more important and complex. Because the calculation is just a simple formula process, it does not depend on the accuracy of the formula itself, but on the accuracy of the given process parameters. Selection involves much more; a little mistake will result in improper shape selection. It will not only waste human, material, and financial resources, but also result in a number of usage problems such as reliability, life expectancy, and operational quality.