Competitive Edge of New Sanitary Pump Designs
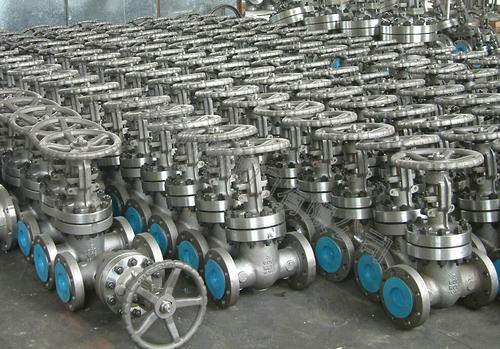
Economic pressures are forcing pharmaceutical manufacturers to look for ways to become more competitive. Many companies realize that they need to reduce their operating costs while maintaining or improving the quality of products.
Recognizing the needs of their customers, many OEM manufacturing engineers write specifications to ensure that the latest innovations will reduce energy consumption, reduce product waste and minimize maintenance requirements. These specifications also improve construction, documentation, and test materials while providing the necessary sterility for critical processes.
Manufacturers of sanitary pumps for the pharmaceutical industry have recently developed options to help meet the needs of the industry, including the following examples:
- Single-seal piping arrangements for internal seals eliminate the need for dual mechanical seals and product flushing piping arrangements. These arrangements save money because they do not use the product as a means of rinsing. This configuration option also creates a high pressure in the low-pressure seal area to prevent the hot product from “flashing” or pitting on the seal faces and increasing the life of the seal.
- Sealing piping designs require lower flushing rates than traditional pumps. For example, some models require the outer seal to be rinsed at flow rates of 2 to 3 gal/h (rather than flow rates of 10 to 20 gal/min) prior to draining.
- The new pumps feature front-loading seal configurations that can be serviced quickly. These pumps do not need to be removed from the line for joint changes. This option reduces the downtime required for maintenance.
- Liquid ring pumps for clean-in-place (CIP) return applications retain their priming, unlike standard centrifugal pumps, which sometimes become airy. Liquid ring pumps are more efficient and less wasteful for the complete evacuation of tanks and pipelines during CIP processes.
Increasingly stringent documentation requirements for pump building materials and component traceability put pressure on the industry. In response, some manufacturers are burning the metal manufacturer’s heat numbers on all of their wet metal components to facilitate traceability.
The new regulations generally require ferrite testing, basic vibration testing, X-ray verification, certified performance and suction head testing, certified finishing mapping, drainage testing, hydrostatic testing, certification of welders, and noise tests. The tests ensure that the pumps will meet the material and performance specifications.
Recognizing the need for drug manufacturers to have cost-effective production processes and their goal of creating high-quality products, pump manufacturers are continually seeking innovation. Their engineers seek to provide highly efficient pumps that require minimal maintenance and provide maximum cleanliness.
By combining their efforts, pump manufacturers and pharmaceutical manufacturers can achieve their common goal of providing safe and effective medicines to patients around the world.