Why do Safety Valves Fail?
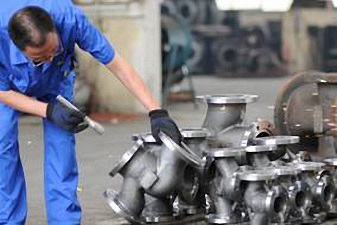
Common Failures of Safety Valves
Valves of all types are critical components of the fluid, gas, and slurry processing systems that we depend on for production, dispensing, plumbing, and so many more essential activities. Our society truly depends on valves to function efficiently — safety valves are considered by many to be the most important.
From time to time, safety valves fail, no matter how well we take care of them. Oftentimes, we don’t realize how important safety valves are until they’re not working properly. Let’s take a look at the most common reasons why safety valves fail.
Six Common Causes of Safety Valve Failure
1. After discharge, the valve flap doesn’t return to its normal position
This is mainly caused by the spring bending the valve stem, incorrect installation position, or jamming of the valve flap. Check for all of these issues, replace any parts as necessary, and reassemble the valve.
2. Valve Leakage
If leakage exceeds the allowable level between the valve flap and the sealing surface of the sanitary valve seat under normal working pressure, it’s usually caused by built-up debris between the valve flap and the valve seat’s sealing surface. In this case, use the lifting wrench to open the valve several times, removing all debris. If the sealing surface is damaged, repair it using the grinding method according to the level of damage. If the valve stem bends, tilts, or if the lever and fulcrum skew, displacing the valve core and valve flap, you should reassemble or replace it. If the elasticity of the spring is reduced or lost, replace the spring and readjust the opening pressure.
3. The valve doesn’t open when the specified pressure is reached
The reason for this kind of failure is that the pressure setting is not accurate. You should readjust the amount of spring compression or the location of the hammer. If the valve flap is stuck to the valve seat, you should begin testing the safety valve regularly for gas exhaust or water discharge. If the safety valve lever is stuck or the hammer has moved, you should readjust the position of the hammer so it allows the lever to move freely.
4. Exhaust is released effectively but pressure continues to rise
This problem normally occurs when your selected safety valve’s exhaust capacity is too small to safely discharge the system’s pressure. In this case, you should reselect a suitable safety valve that accommodates your necessary pressure levels. If the centerline of the valve stem is not upright or the spring rusts, causing the valve flap to fall short of the required height, you should reassemble the valve stem or replace the spring.
5. Frequent jumping or excess vibration of the valve flap
This is mainly because the stiffness of the spring is too large. In this case, we should use a spring with proper stiffness. If the adjustment ring is not properly set up, it can lead to excess pressure on the valve seat. In this case, you should readjust the adjustment ring’s position. If the resistance of the discharge pipe is too large, causing overly large discharge back pressure, you must reduce the resistance of the discharge pipeline.
6. The safety valve opens below the specified pressure
This is mainly due to the inaccurate pressure settings and aging springs, leading to reduced elasticity. In this case, you should properly tighten the regulating stem or replace the spring.
Conclusion — Safety Valve Failure
Valve leakage is one of the most common faults of boiler safety valves. It mainly refers to leakage between the valve disc and the valve seat under normal working pressure. If you experience any problems with your safety valves, please contact us and we will be happy to help you resolve them.