Common Failures of Automatic Valve
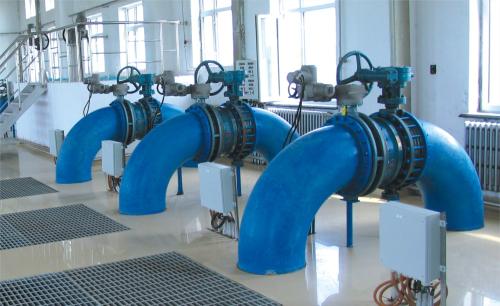
Four common failures associated with automatic valves are found at a high frequency in poorly performing control loops. These are Dead band, Stiction, Positioner overshoot, Incorrect valve sizing, and Nonlinear flow characteristic. Let’s take a closer look at each of these problems.
Failure one: the valve is blocked up.
The reasons are:
1. The control channel is blocked by debris.
2. The piston is stuck at the highest position due to rust. Although its upper part is impacted, the piston can’t move down, unable to open the main channel.
Therefore, filters must be installed before sanitary pressure relief valve. For pressure relief valves that are newly installed or seldom used for a long time, be sure to open them for inspection and cleaning.
Failure two: The valve is straight-through, providing no pressure relief effect.
The reasons are:
1. The piston is stuck at a certain (not the highest) position.
2. The main valve stem is stuck at a certain (not sealed) position of the cylinder disc guide hole.
3. The lower spring of the main valve flap is broken or malfunctioned.
4. The pulse valve stem is stuck at a certain (not sealed) position of the valve seat hole so that the piston is always under pressure.
5. There is dirt or scratch between the two sealing surfaces of the main valve flap and main valve seat.
6. Diaphragm malfunctions due to wear or damage.
For pressure relief valves, regular inspection should be performed. Dirt and rust stains should be promptly removed; damaged piston ring should be replaced; malfunctioned spring should be replaced; re-grind the sealing surface if it’s not airtight; damaged diaphragm should be replaced; polish the valve stem using sandpapers if it’s confirmed to be rather thick.
Failure three: the pressure behind valves can’t be regulated.
In addition to the above reasons, there are also:
1. Regulating spring malfunctions.
2. Cap seam leakage, unable to maintain pressure.
These also need to be prevented by prompt check-ups.
In addition, there is a phenomenon: pressure pulse behind the valve fluctuates, highly unstable.
This is because the difference between the input medium and the output medium is too large. We should re-select the valve with the appropriate valve diameter. Another reason causing unstable pressure behind the valve: improper selection of regulating spring.
There’re several kinds of regulating springs for a pressure relief valve of nominal pressure. For instance, the nominal pressure is 16 kg per square centimeter, there’s 1-3 kg per square centimeter, 2-8 kg per square centimeter, 7-11 kg per square centimeter for the regulating spring. If the pressure behind the valve is only 1-3 kg per square centimeter, while the spring is 7-11 kg per square centimeter type, then the pressure behind the valve can’t be accurately regulated.