Anti-corrosion Treatment of Stainless Steel Sanitary Fitting
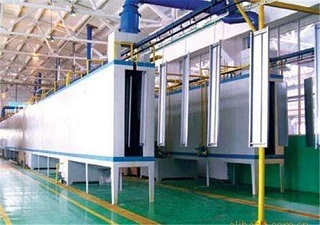
The 316L stainless steel sanitary fittings contain 50% iron and 10.5% chromium, and nickel, titanium, and molybdenum are also added. The metallographic structure of metal varies according to its different chemical compositions. Thus, there are a variety of types of stainless steel, such as martensitic, ferritic, austenitic, duplex, and precipitation hardening.316L stainless steel sanitary fittings also have different materials.
Commonly used material
In general, austenitic stainless steel tubes are used in many industries. The selection of 316L stainless steel sanitary fittings is related to the type, concentration, temperature, pressure, flow velocity, fluid medium, and so on.
The heat treatment process of 316L stainless steel sanitary fittings
The 316L stainless steel sanitary fittings are annealed in the temperature range from 1850 to 2050 degrees, and then annealed and cooled rapidly, since the 316 stainless steel cannot be superheated for hardening.
In the stamping process of SUS304 stainless steel, it is necessary to carry out the softening annealing, which is also called intermediate annealing. In order to obtain the best corrosion resistance, the welding section of 316 stainless steel sanitary fitting needs to be annealed after welding. If 316L stainless steel sanitary fittings are used, post-welding annealing is not required.
Corrosion-resistant treatment of the surface of stainless steel sanitary fittings
The inner and outer surfaces of stainless steel sanitary fittings (especially after electropolishing and mechanical polishing) have a good passivation layer and strong corrosion resistance. A high surface finish and little medium adhesion are conducive to corrosion resistance. The less liquid media trapped in the inner surface of the pipe with a high finish, the better for flushing, especially in the pharmaceutical industry.
1. Electrochemical polishing of the inner surface of sanitary fittings
Electrolytic polishing fluids mainly are phosphoric acid, sulfuric acid, chromium anhydride, gelatin, and potassium dichromate. The inner surface of the stainless steel sanitary fittings is on the anode, and the polishing liquid flows through the anode and the inner surface of the stainless steel fittings at a low voltage and a high current so that it can be electropolished. At this time, two contradictory processes are going on the inner surface of the fittings, that is, the formation and dissolution of the passivation layer (including the thick mucosa) on the metal surface.
Due to the difference of the conditions for the film-forming of the micro convex part and the concave part of the surface to enter the passivation, as well as the anodic dissolution, the concentration of metal salts in the anode area keeps increasing, forming a kind of high resistance thick mucosa on the surface. The thickness of the film in the concave and convex places leads to the high current density on the surface of the anode and the rapid dissolution of the tip discharge, which can achieve the purpose of flattening prominent micro parts in a short time and can achieve a high degree of smoothness Ra≤0.2-0.4μm. Under this action, the chromium content in the inner surface of the stainless steel sanitary fittings is increased, and the corrosion resistance of the passivated layer on the metal surface is also increased.
How to master the polishing quality depends on the electrolyte formula, concentration, temperature, power-on time, current density, electrode condition, and the degree of surface treatment of sanitary fittings. If the technology is not well mastered, the surface smoothness of the tube will be damaged. Or if the electrolysis degree is too high, more and larger concave and convex surfaces will appear and even the fittings will be scrapped.
2. Mechanical polishing of the inner surface of the sanitary fitting
Mechanical polishing of the inner surface of the sanitary fitting includes rotary and linear polishing. Take rotary mechanical polishing as an example, the mechanical polishing equipment is relatively simple, and it adopts the cloth plate made of fine sand step by step, and the cloth plate is polished many times on the inner and outer surface of the pipe, and the smoothness can reach Ra≤0.2-0.4μm.
Compared with electrolytic polishing, mechanical polishing has the advantages of simple equipment, low technical content, ease to master, and low cost. In addition, it will not destroy the fittings and cause scrap, so it is widely used.
Please visit http://www.adamantvalves.com for more information.