What is a Balanced Sleeve Type Pressure Relief Valve?
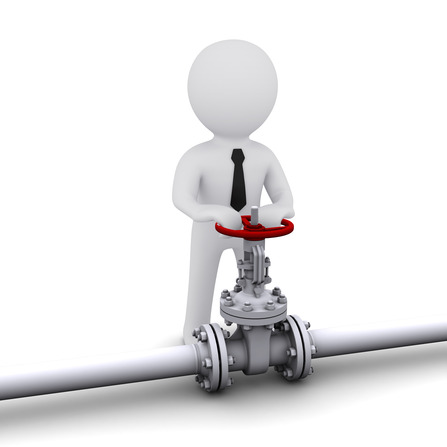
What is a pressure relief valve?
The pressure relief valve is a kind of self-powered regulating valve. It throttles using a valve member, reducing the inlet pressure to the desired outlet pressure. When the inlet pressure and the amount of flow change, it relies on elastic components and the power of transmitting the medium to keep the outlet pressure largely unchanged.
What are the types of sanitary pressure relief valves?
The commonly used sanitary pressure relief valve is usually level one throttle whose valve flap is cone-shaped. The pressure relief valve of level one throttle has a better effect under the low-pressure drop. Under high-pressure drop, cavitation is prone to occur, which will lead to premature damage of throttling members. In light of this, two or more pressure relief valves are often used in parallel, which increases the operating cost of the system and the instability. In order to solve the problem of pressure-relieving under the high-pressure drop, a kind of two-stage throttle balanced sleeve type pressure relief valve was designed.
According to structural forms, the pressure relief valve can be divided into direct-acting film type, direct-acting bellows type, pilot film type, pilot bellows type, and pilot piston type. Regardless of the structural form, they all automatically balance the pressure of the medium using the elastic component to regulate the opening of the valve flap to throttle and reduce pressure.
What is Balanced Sleeve Type Pressure Relief Valve?
The valve flap is the core component of the pressure relief valve. Whether its design is reasonable or not directly affects the operating performance of the pressure relief valve.
The valve flap of the pressure relief valve uses two-stage balanced sleeve type throttle. In the middle of the valve flap, six throttle holes of the same area are drilled and are evenly distributed circumferentially. These are level two throttle holes. The medium enters the cylindrical space of the valve flap from the inlet of the pressure relief valve, through the six throttle holes in the middle of the valve flap. Because the upper and lower area of the cylindrical space is the same, the liquid pressure sustained by the upper and lower sleeves is offset to reach a balance. Thus, the area of throttling is not affected by the change in the pressure of the inlet. Then, the medium enters the outlet of the pressure relief valve through the upper and lower throttle holes.
The total area of the upper and lower twelve two-stage throttle holes is the same as the total area of the six first-stage throttle holes in the center. Two-stage throttling pressure is close, that is, the total throttling pressure of the pressure relief valve is basically evenly distributed, which controls the speed of the liquid flow. In addition, the respective six throttle holes at the upper, middle, and lower parts are circumferentially positioned, eliminating the lateral force.
A two-stage throttle balanced sleeve type pressure relief valve has many advantages:
1. Two-stage throttling can be achieved, which solves the problem of pressure reducing under the high-pressure drop, alleviates the hydraulic shock, avoids cavitation, and lowers the noise. It can also be used to reduce pressure under a low-pressure drop.
2. Through simple structural design, the valve flap is horizontally balanced while being vertically balanced, which reduces the cost of design and manufacturing.
3. The lateral thrust of the valve flap is balanced, the piloting is smooth, the service life of the sealing surface of the valve seat improves, the structural optimization is reasonable.
4. The valve flap can be quickly disassembled in whole, which is easy for repair and maintenance.
5. The elastic component only corresponds with the outlet pressure of the two-stage throttling, which can improve the stability of the outlet pressure.